Yellow Belt
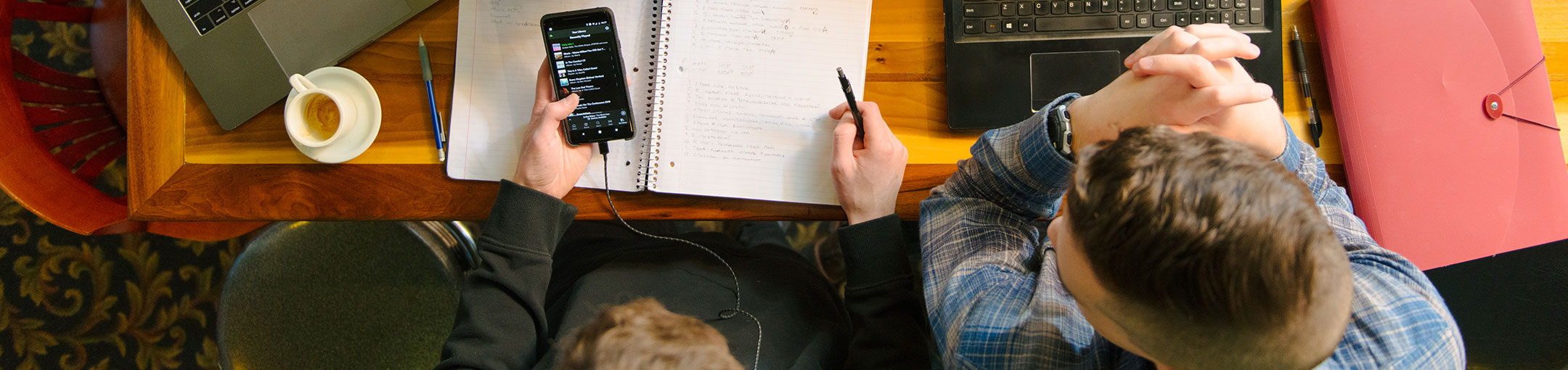

Yellow Belt – contract
- RIT/
- Center for Quality and Applied Statistics/
- Lean Six Sigma/
- Yellow Belt – contract
Learn the fundamentals of Lean Six Sigma while addressing a real process problem!
A contract program for groups and organizations that can be customized and delivered on-site or in a blended online format. Contact us at cqas@rit.edu for more information and a quote.
CQAS's Lean Six Sigma Yellow Belt Certification training program is a powerful workforce development activity focused on team-based problem solving! It is built around a core group of process improvement tools designed to help professionals solve job-related problems more efficiently and effectively by utilizing these tools within a structured methodology.
During this highly interactive program, participants will apply process improvement tools on a real problem of your own while following the first four phases of the DMAIC process: Define, Measure, Analyze, and Improve. At the end of the program, teams will craft a set of recommendations that are ready for consideration by management. Managers are encouraged to attend final presentations. Upon completion of the program, each participant will be certified by CQAS as a Lean Six Sigma Yellow Belt.
On-Site Program
Our on-site program is usually delivered in 3 consecutive days. Attendees are exposed to each topic in-depth through interactive discussions, structured exercises within a team environment, and application of tools to a real project.
Blended Online Program
Our blended online program covers the same content as our on-site program but is offered over a 3-week period in a format that is flexible to participants' work schedules. Learning materials include pre-recorded lectures, team exercises, and quizzes; online “discussion boards”; and “live” project review sessions via web-conference to discuss team exercises and offer feedback on each team project. A live interactive orientation session is held to provide attendees the opportunity to meet their instructors and classmates, navigate our online learning platform, understand course expectations, and answer questions. Unlike self-paced online training, our instructor-guided approach keeps participants actively engaged while still providing flexibility to meet their other commitments.
Topics
- Lean Six Sigma Enterprise Approach to Improvement. By integrating complementary concepts and tools from both the Lean and Six Sigma bodies of knowledge, we've crafted a more powerful toolbox to address challenging problems and generate more impactful results. Attendees will learn about the history of each methodology and how they effectively complement each other. They will be introduced to the nine wastes and five stages of the DMAIC improvement process – Define, Measure, Analyze, Improve, Control – as well as key tools associated with each stage.
- Problem Solving Process/Tools. Learn how to define a problem, determine root causes, and identify and implement strategies for improvement. These tools are designed to help teams understand a problem, organize information, and reach consensus.
- Statistical Thinking. Lean Six Sigma focuses on connected processes, and the primary objective is to reduce process variation or unpredictability of outcomes. Examples will be heavily utilized to provide a working knowledge of data-driven thinking and how to become a “process thinker” focused on reducing variation.
- 5-S and Visual Controls. Learn how to implement a sustainable 5-S program: the steps in 5-S, what a 5-S audit should look like, and a classroom simulation to reinforce the fundamental concept of 5-S and why it is not simply a “clean-up” program. Examples of visual controls will show how to apply these concepts to real-world problems and opportunities.
- Change. Improvement involves change and change can be challenging. We will discuss the underlying reasons for the failure of most change initiatives, and how to develop strategies to create an environment within which change can be successfully implemented.
Certification
Certification by CQAS as a Lean Six Sigma Yellow Belt requires successful completion of training including all course materials and deliverables and participation in discussions and final presentation.
Contact us at cqas@rit.edu for more information and a quote.
FAQ's
The program is structured around teams and is a great opportunity to work on a shared problem with others in your organization or in other organizations.
It is not required to have projecs in advance but it is helpful to identify opportunities that can be addressed during the training. If projects are needed, the instructor will facilitate project identification during orientation and each team will work on a process improvement opportunity during the program.
Our online format is designed to provide flexibility so that participants can meet their other commitments from wherever they are while insuring active engagement with our instructors and other program participants.
Our on-site programs generally consist of three consecutive days. Blended programs (online + on-site) require approximately the same time commitment (1-2 hours of training content and 5-6 hours on a team project per week) but this commitment is spread out over several weeks.
Yes. Upon request, participants will be issued 2 CEU’s at the end of the program.