Cooling High Performance Computing Processors in Data Centers with Boiling Chamber
With a rising need for high-performance computing in data centers, enhanced heat dissipation from the microprocessors becomes critical for maintaining their surface temperature in a compact setting. The present work investigates enhancing liquid cooling with subcooled boiling and submerged condensation in a novel subcooled boiling chamber.
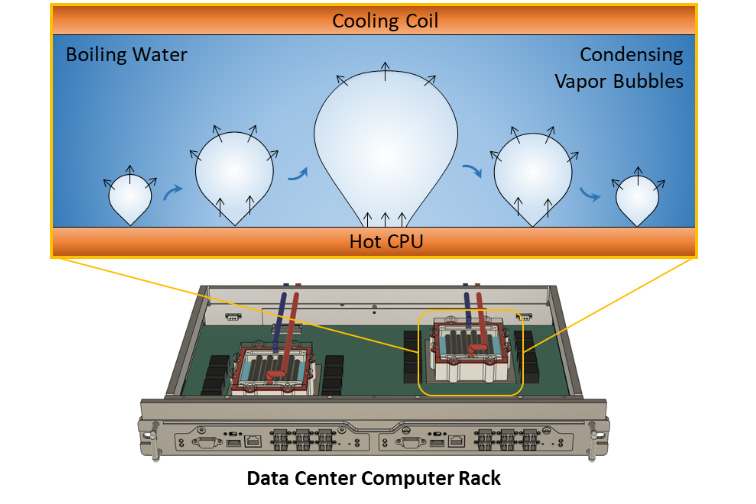
With a rising need for high-performance computing in data centers, enhanced heat dissipation from the microprocessors becomes critical for maintaining their surface temperature in a compact setting. Factors like high Thermal Design Power (TDP), small footprint and constricted packing make thermal management of CPU/GPU challenging. While air cooling has been sufficient until now, liquid cooling proves to be superior in its heat dissipation capabilities. However, a cooling method technique with a high heat transfer coefficient and low thermal resistance is highly desired to reduce energy consumption in transporting this heat. The present work investigates enhancing liquid cooling with subcooled boiling and submerged condensation in a novel subcooled boiling chamber.
Compared to pool boiling, where a condensing coil condenses vapor above a pool of boiling liquid, the novel boiling chamber submerges the condenser coil partly in the liquid pool and the vapor space. Submerging the condensing coil enhances boiling by augmenting subcooled boiling and enhanced vapor condensation through submerged condensation and direct contact cooling. Moreover, it allows the boiling chamber to be compact enough to pack in 1U and 2U servers of a data center rack. Preliminary experimental testing on a thermal test vehicle was performed to validate the enhanced thermal performance of the boiling chamber and understand the heat transfer mechanisms at work. While the novel boiling chamber resulted in high heat dissipation using 3M Novec 7000 dielectric fluid, the results of testing with water are shown below.
When testing with water, the results show that the boiling chamber can dissipate more than 1.1 kW of heat from a simulated CPU having a 34.5 × 32 mm2 surface area. Comparing the advantages of subcooled boiling and submerged condensation with saturated boiling, it becomes clear that the novel boiling chamber can reduce the surface temperature while dissipating large quantities of heat. When testing with 40% fill volume, the device prototype dissipated more than 880 W (q” = 79.7 W/cm2) of heat with a thermal resistance lower than 0.06 °C/W while keeping the surface temperature below 92 °C.