School of Media Sciences MS candidate presents research
Chandramohan Seetharamiah Srinivasaraju, center, is joined by RIT Print and Postal HUB managers Christian Argentieri, left, and Mark Soman at his thesis research presentation.
Chandramohan Seetharamiah Srinivasaraju, a candidate of RIT School of Media Sciences’ print media MS program, presented his thesis research at a colloquia held on Jan. 21.
Advised by Gravure Endowed Professor Robert Eller and associate professor Gregory S. D'Amico, Ph.D., Seetharamiah Srinivasaraju, who prefers to be addressed as Chandra, analyzed print quality aspects of printed targets made from new RotoHybrid gravure cylinders versus conventional gravure cylinders.
According to Chandra, gravure printing has been steadily losing market share in North America to flexographic printing technologies. Among the reasons cited for this decline are preparation costs and the time entailed to produce a conventional gravure cylinder. Further, it is noted that producing conventional gravure cylinders is not an especially environmentally friendly process, largely due to the chrome utilized.
Chandra indicated that fumes and liquid waste from the chromium process can pollute air and water, and are not biodegradable. Further, the process involves known carcinogens. For these reasons, printers normally rely on third-party trade shops to engrave conventional cylinders, rather than assume these tasks in-house. This process also adds time to the conventional gravure workflow.
A new gravure cylinder technology, known as RotoHybrid, promises to address these concerns, Chandra said.
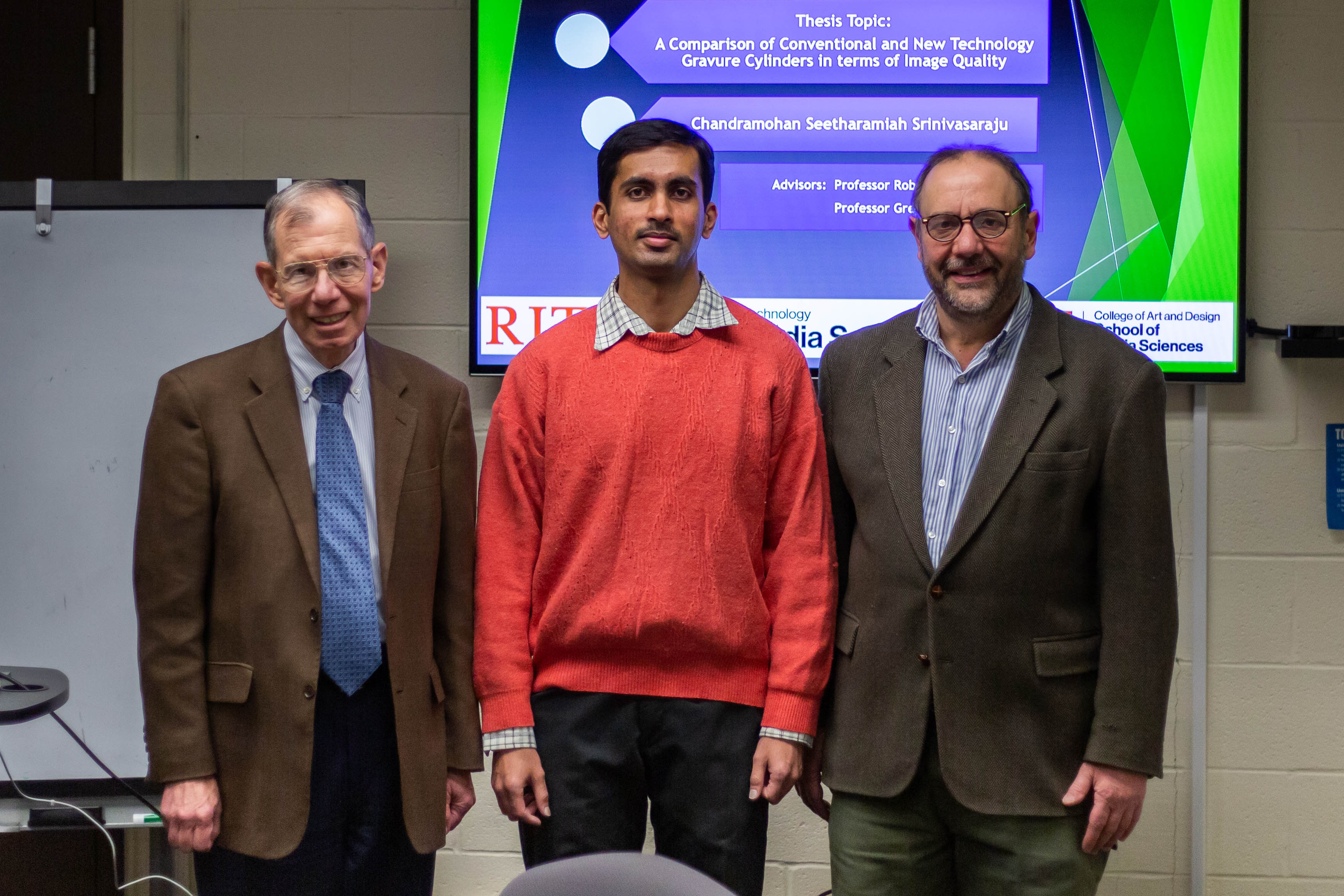
RotoHybrid cylinders utilize a "hybrid chrome replacement" (HCR). HCR is based on a "diamond-like carbon,” a man-made synthetic carbon that meets the protective characteristics of chrome, while having the selective characteristics of graphite, with the hardness of industrial diamonds. Compared with conventional gravure cylinders, the process of engraving HCR cylinders is simpler and much more environmentally friendly.
The research question Chandra addressed, therefore, is: "How does the Image Quality of New Technology Gravure Cylinders compare to the Image Quality of Conventional Gravure Cylinders?"
Working together with Eller, Chandra developed a testing protocol using the Betaflex3Pro to analyze aspects of both dot quality and line quality.
Dot quality attributes tested included dot surface area, minimum printed dot and dot roughness factor. Tested line quality attributes included conformance to a specified line width, thinnest consistently printable lines and pugging of reverse printed lines.
Relative solid ink density as measured by a Techkon SpectroDens was also evaluated. In each tested attribute, Chandra reported that the HCR technology either equaled or outperformed the conventional cylinder counterpart.
The reported implications for the results of this study can be profound: it is believed that more printers can adopt the ability to produce HCR cylinders in-house, without sacrificing image quality. In fact, Chandra indicates that printing quality can actually be improved above the already high bar set by gravure printing with conventional cylinders. His results also suggest that ink savings can be realized with HCR cylinders.
Having completed his thesis research, Chandra is working closely with Eller on a next phase of research in this domain, including examining the performance of the RotoHybrid gravure cylinders in an exhaustive wear test in Western Michigan at the end of January. This test will pit the new RotoHybrid cylinder against conventional gravure cylinders using opaque white ink, perhaps the most abrasive of all the inks normally used in this application. This testing aims to address a stated limitation of Chandra's thesis, which was comparing the print quality of the tested cylinders when new.
Chandra is also working at the RIT Print and Postal HUB this semester, where he is gaining insight into digital and offset lithographic printing processes in a production environment.