Ex One Co. Donates Additive Manufacturing Equipment to RIT Brinkman Lab
New customization process has potential to trigger manufacturing resurgence
David Burns
Manufacturing is moving beyond assembly lines that make standardized products to customized equipment and parts. The demand for customization may best be met by the growing trend of additive manufacturing—and the next generation of engineers able to utilize the technology.
The Ex One Co., a national manufacturing organization, has donated a ProMetal RX-D 3-D printer to the Earl W. Brinkman Laboratory at Rochester Institute of Technology. The equipment will serve as a teaching tool for RIT’s students and as a resource for campus researchers striving to further the breakthrough technology.
The 3-D printer is a key component of today’s additive manufacturing technologies, which have evolved from rapid prototyping and other three-dimensional laser technologies.
According to David Burns, president of Ex One Co., RIT is positioned to be a leader in the further development of additive manufacturing due to its digital printing, optical capture and micro-engineering capabilities. All the foundation, or predecessor technologies, to develop additive manufacturing techniques can be found at RIT, he says.
“RIT is a world leader in research in both optical capture and conversion to digital modeling. The necessary steps that precede additive manufacturing are the creation or capture of digital information. No matter how you get it, either capture it or create it, RIT is right on the leading edge of those technologies,” says Burns, a member of the RIT Board of Trustees and former chief executive officer of Gleason Corp.
Early developers of additive manufacturing technologies used plastics and other composite materials to build prototypes of equipment such as automobile parts. Using a computer-aided design technology, the objects are drawn, first through 3-D imaging and optical capture, then input into the 3-D printer. The machine prints layer-upon-layer of the object. Today, some companies, including Ex One, have capabilities to develop products using glass or metals through the additive manufacturing process.
“Although we have had the ability to print plastic parts in the Brinkman Lab for some time now, this donation is very exciting in that it will allow us to directly print metallic components for the first time,” says Denis Cormier, the Earl W. Brinkman Professor of Machining and Manufacturing in RIT’s Kate Gleason College of Engineering.
Cormier is one of the foremost scholars in the area of additive manufacturing. He is working on a research project funded by the U.S. Department of Energy for “Science-based Nano-structure Design and Synthesis of Heterogeneous Functional Materials for Energy Systems.” The research continues his work in rapid prototyping and additive manufacturing with a focus on printing nano-inks to produce energy devices such as fuel cells and batteries.
“Additive manufacturing, by its definition, means that you can make precisely what you want, when you want it, in the quantity that you want, and it gives manufacturers the opportunity to have each separate piece be uniquely configured,” says Burns. “So with the culture of the U.S, where we are depending more and more on speed and customization, it is a remarkable field to study. At the end of the day, additive manufacturing may be about the re-emergence and survival of the manufacturing base in this country.”
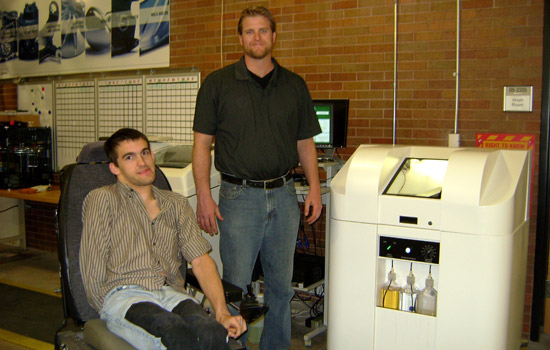