Using 3D Printable Density-Graded Lattice Structures to Minimize Risk of Tissue Damage from Compression-Release Stabilized Sockets
Designing safe and effective upper limb prosthetic sockets requires knowledge of the complex interplay between a person’s individual anatomical features and their interface with a prosthetic device. If not fitted correctly, damage can occur within the soft tissue of a person’s residual limb. In this research, we consider a novel strategy to minimize the risk of soft tissue damage in a modified prosthetic socket design.
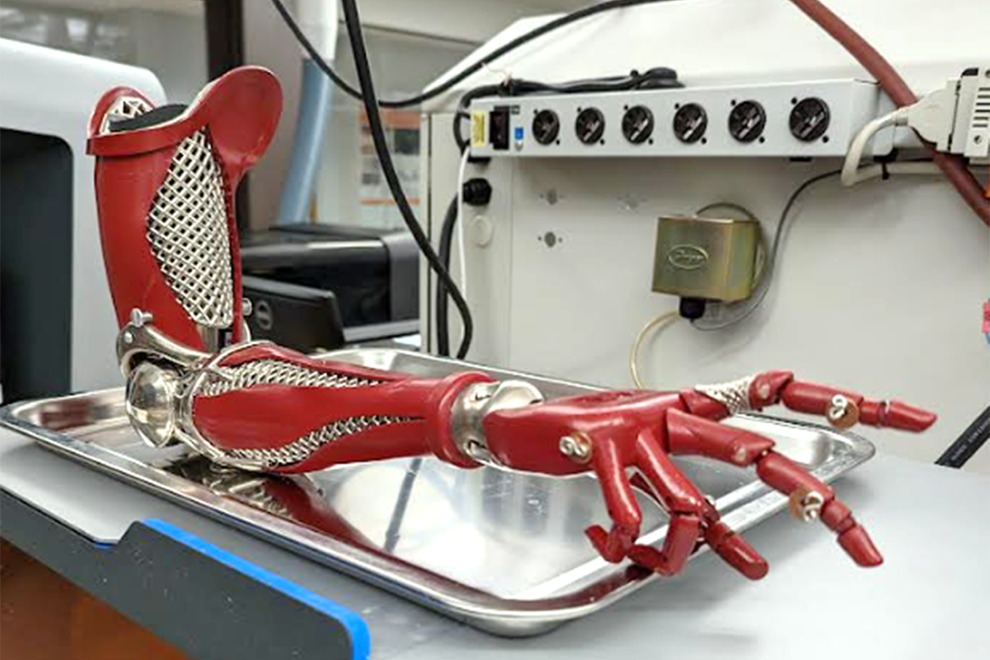
For people with amputations, prosthetic sockets are the critical interface where their residual limb meets the prosthetic device. For a socket to perform as it should to stabilize the prosthesis on the body, provide utility, offer comfort, and prevent injury from things like unintended twisting or tissue damage, the socket must be fitted by a trained clinician according to an individual’s specific anatomical features. Different approaches to socket design are currently being used in practice, each with a unique set of benefits and drawbacks. While Compression-Release Stabilized (CRS) sockets show promise in that they allow users the benefits of effective stabilization, increased control over their prosthesis, and a reduction in sweating, there remains a risk for tissue damage in the residual limb from large changes in compression over short distances within the socket. In this research, we investigate the use of 3D printable density-graded lattice structures as a strategy for mitigating tissue damage in a modified CRS socket design by allowing more gradual transitions from areas of compression to areas of release within the socket.
This research was supported, in part, through funds from the Orthotic and Prosthetic Education and Research Foundation, Inc. (OPERF), and was conducted by mechanical and industrial engineering Ph.D. candidate, Jade Myers under the advisement and expertise of Drs Dan Phillips and Denis Cormier. Jade has accepted the position of Research Development Specialist within RIT’s AMPrint Center, and also serves as an Adjunct Professor within the School of Individualized Study and the Kate Gleason College of Engineering.