Doctoral Student Revamps Machining Training to Boost Workforce
RIT doctoral student Krzysztof Jarosz, guided by Dr. Rui Liu, is pioneering improvements in machining training programs to address workforce shortages by making training more engaging and effective in preparing the next generation of machinists.
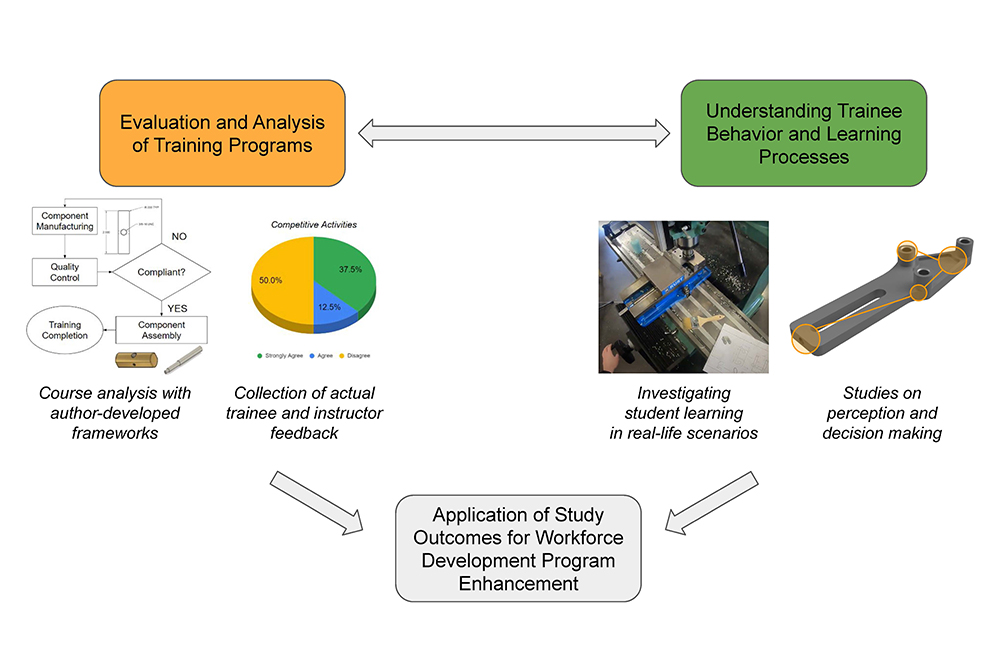
Widespread adoption of Industry 4.0 standards and technologies in the machining industry has resulted in machining processes becoming increasingly machine-centered, automated, and “smart”. However, this state-of-the-art equipment still requires a skilled workforce to operate it. As experienced machinists age and retire and interest in machining careers declines in younger generations, there is a workforce shortage that negatively affects this vital sector of the economy. According to the Bureau of Labor Statistics data, the machining industry has experienced a staggering shrinkage of 13% merely within the timespan of two years. One of the underlying causes of this complex issue is the nature of current training programs, which focus heavily on lecturing mixed with repetitive and mundane hands-on activities at the expense of student motivation and engagement, making trainees disinterested in pursuing machining related careers. Despite serious implications of the problem, investigating the possibilities of evaluating outdated workforce development practices and devising methods to improve them have not attracted sufficient prior research attention.
The main objective of this research is to address this gap by thoroughly evaluating and improving the extant machining workforce development programs. Main research questions investigated include the following:
- What are the shortcomings of current training methods and how can they be improved?
- What techniques and mechanics are most appropriate for improvement of machining workforce development programs?
- How said mechanics can be implemented effectively?
- How can learning outcomes of said programs be assessed and measured objectively and robustly?
Under the supervision and guidance of Dr. Rui Liu from the Smart Manufacturing Research Group laboratory at RIT, doctoral student Krzysztof Kamil Jarosz has been conducting numerous research efforts associated with aforementioned topics. The relevance and anticipated impact of this work lies in helping to attract new prospective professionals to the industry, mitigating the adverse effects of shrinking and aging machinist population. Employed methods include 1) experimental studies to investigate trainee behavior, perception, learning and decision making 2) student/instructor surveying and curriculum evaluation to identify key areas for training program improvement and 3) application of behavioral/cognitive study outcomes along with appropriate gamification frameworks to enhance current training programs. The outcomes from application of those methods are to serve the primary goal of improving the current workforce development and training programs by making them more efficient, attractive and engaging for prospective employees in the machining industry.